Namib Lead Zinc Mine Bankability Strengthened Significantly following completion of further Metallurgical Testwork
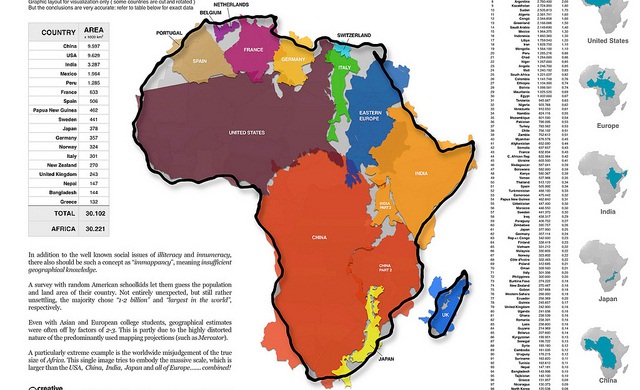
North River Resources has announced that, following supplementary metallurgical testwork, confidence in the planned ore processing solution for the Namib Lead Zinc Project in Namibia has been improved significantly.
Highlights:
· A critical milestone as North River moves towards the construction phase at Namib, focused on developing a 250,000 tonne per annum operation
· Ore processing flow sheet defined, which eliminates variability associated with the previously proposed process and ensures a robust operating environment for future planned production
o Main variables in mineralogy and flotation chemistry now accounted for
o Most effective grind size and metallurgical route now determined
· Delivering increased confidence in expected concentrate grades and recoveries with results from wide ranging ore composites conducted under simulated plant conditions
o Lead (‘Pb’) concentrate grade of at 62.2% at 91.1% Pb recovery, and
o Zinc (‘Zn’) concentrate grade of 52.4% Zn at 89.2% Zn recovery
North River CEO James Beams said, “The optimisation work carried out by independent experts provides the Company with a definitive and robust processing solution for our stand-out Namib Lead Zinc Mine in Namibia. The improvement in operational control, that this process flow sheet provides, will add significant value to our preparations for Front End Engineering and Design ahead of a construction decision. I look forward to providing further updates as we incorporate this plant design into the operating model for the Namib mine.”
Overview of the Metallurgical Testwork Programme:
Background
In January 2015, North River appointed ALS Laboratories to conduct a detailed supplementary testwork programme. ALS was selected for their relevant experience and knowledge of similar milling operations. The work was conducted to address the inconsistent grade recoveries experienced via processing routes proposed as part of the Definitive Feasibility Study which referred to a ‘lack of agreement’ on the performance of different samples.
The lack of a definitive processing solution in the DFS derives from the fact that the mineralisation at Namib contains the iron sulphide mineral, pyrrhotite, which responds to flotation in a similar manner to the minerals, sphalerite and marmatite which are the primary zinc ore minerals at Namib. This response can lead to a build-up of pyrrhotite, and consequently iron, in the zinc cleaner circuit. While iron is common in lead-zinc deposits, it is normally present as pyrite, which can be more easily depressed during flotation than pyrrhotite.
The implications of the presence of pyrrhotite were experienced first-hand in the previous operation and, as a result, intermediate products had to be dumped to tailings in order to maintain saleable concentrate quality, but at the sacrifice of zinc recovery during processing.
At the time of publication of the DFS, the locked cycle tests which were underway had not yet been completed. The DFS postulated that the use of magnetic separation as a means of removing some of the pyrrhotite from the circuit, but the subsequent results did not support this proposal as zinc recovery was compromised. Therefore the focus of the latest work was to produce a robust operating environment, taking into account the main variables in mineralogy and flotation chemistry.
Optimisation Work
To properly liberate the generally finer zinc minerals, a separate zinc regrind circuit is required to optimise the overall zinc recovery and concentrate grade. Extensive mineralogy was conducted as a precursor to flotation testwork to determine the most effective grind size. A primary grind of around 80% passing 100 micron level has been selected and this is also a practically achievable level within the proposed processing system.
Following this, the fundamental issue in improving the differential flotation performance was the selection of an optimal reagent regime. The use of zinc sulphate as a reagent, commonly used in other lead/zinc operations, was identified as a major contributor to slowing down the sphalerite recovery rate making effective separation from the pyrrhotite more difficult. Consequently, testwork was necessary to eliminate zinc sulphate from the flowsheet and identify a more selective lead collector. These newer collectors, replacing the more traditional xanthates and zinc sulphate, have proved successful in the testwork.
Using the optimised grind and new reagent regime, the Company has developed a robust processing methodology which can operate with consistent results with a wide range of mineral composition and particularly with the variable pyrite and pyrrhotite content.
This different regime has given reproducible results using locked cycle tests conducted to complete equilibrium. Overall the reproducible results, from the five different composites tested, gave the following results:
· Lead: 62.2%Pb at 91.1% Pb recovery
· Zinc: 52.4%Zn at 89.2% Zn recovery (optimum Zinc grades limited by the zinc mineral Marmatite which has a high iron content)
These are actual results with the top and bottom values discarded from compatible locked cycle tests. This has obviating the previous problem of using batch data when the concentrate grade and associated recoveries can be mutually unsustainable.
Detailed minor element analyses of the above reported concentrates show no impurities that could affect the marketing acceptability.
These results are a significant development, removing any residual concern over operational variability in the processing plant and demonstrating robust controls of the final saleable products. This greatly assists in overall project bankability as the Company moves forward with its financing plans and, in particular, its discussions with debt financiers.