VANCOUVER, April 17, 2019 /CNW/ - Victory Metals
("TSX-V:VMX") ("Victory" or the
"Company") is pleased to announce results from initial
metallurgical tests conducted by McClelland Laboratories, Inc.
("McClelland Laboratories") of Sparks, Nevada, on drill cuttings from the
Company's Iron Point Vanadium Project. Test work using
hydrometallurgical processes at atmospheric pressure has yielded
vanadium recoveries in excess of 90% in leach times of less than
eight hours.
Highlights – Phase I Metallurgical Testwork
- Initial bench-scale hydrometallurgical leach testing on Iron
Point RC drill cuttings demonstrate up to 94.3% vanadium recovery
at atmospheric pressure and 8-hour leach times
- RC drill cutting Master Composite used in testing had a median
head grade of 0.38% V205
- 16 preliminary tests were completed utilizing the Master
Composite and varying four test factors: temperature, slurry solids
density, and concentrations of hydrofluoric and sulphuric acid
- Phase II testing is underway that will further define operating
parameters required to develop an economic atmospheric leaching
process for Iron Point vanadium mineralization
Jeff Woods, Victory's Chief
Metallurgist stated: "Preliminary testing last year by McClelland
Laboratories on drill core samples indicated that a low-cost
atmospheric leach may be suitable for Iron Point vanadium
mineralization. A review of published work led to the first
phase of experimental tests released today utilizing RC drill
cuttings. Our preliminary tests confirm that an atmospheric leach
process can successfully recover vanadium at levels greater than
90% with potential for relatively low acid consumption. We are in
the process of augmenting the initial test work to optimize
recovery and minimize operating costs, before starting variability
testing and solvent extraction/precipitation testing."
Paul Matysek, Executive Chairman,
stated: "Initial metallurgical testing conducted at McClelland
Laboratories is very encouraging, creating a pathway forward to a
potentially economic processing route for the Iron Point Vanadium
Project. Importantly, the methods explored are done at ambient
pressure without the use of costly pressure oxidization or
roasting. Furthermore, these hydrometallurgical methods are
commonly utilized in base metal processes and show promise for
applicability to vanadium recovery. Our maiden drilling campaign
clearly outlined a large mineralized system. With promising initial
metallurgical results returned to date, we can work towards
identifying an economic process that will allow us to fast track
towards resource definition and a Preliminary Economic
Assessment."
Phase I Testwork
A total of 197 Reverse Circulation ("RC") drill reject
samples were delivered to McClelland Laboratories of Sparks, Nevada, for sample prep, assaying, and
compositing. McClelland Laboratories, established in 1986, is
recognized as a top mineral-processing laboratory with a focus on
hydrometallurgical extraction of precious and base metals, as well
as specific experience in vanadium metallurgy. Their experience and
knowledge have accelerated the development of Victory's atmospheric
hydrometallurgical process.
A Master Composite sample was constructed using 197 drill
cuttings interval samples that best represented both the spatial
and stratigraphic distribution of mineralized zones throughout the
Iron Point Project as described in Table 1 and shown in Figure 1.
Specifically, the Master Composite is made up of cuttings from
drill intervals ranging between a depth of 1.5 m to 164.6 m.
Intervals incorporated into the composite had a minimum grade of
0.17% V205, a maximum grade of 1.14%
V205, a median grade of 0.38%
V205, and a mean (unweighted) grade of 0.34%
V205 from triplicate analysis.
Table 1: RC Drill
Cutting Intervals used in the Master Composite
|
|
Number
|
Range of Depth
m
|
V2O5 %
|
RC Hole
ID
|
N
|
Min
|
Max
|
Min
|
Max
|
Mean
|
VM-2
|
36
|
9.1
|
164.6
|
0.21
|
0.79
|
0.45
|
VM-7
|
39
|
6.1
|
137.2
|
0.20
|
0.79
|
0.46
|
VM-18
|
31
|
4.6
|
65.5
|
0.21
|
0.64
|
0.38
|
VM-23
|
18
|
1.5
|
85.3
|
0.25
|
0.99
|
0.61
|
VM-33
|
44
|
42.7
|
128.0
|
0.21
|
0.71
|
0.35
|
VM-76
|
29
|
6.1
|
146.3
|
0.17
|
1.14
|
0.42
|
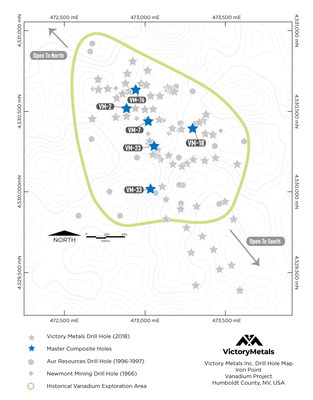
After a review of published work and some early test work on
drill core samples, a Design of Experiments program (DOE) was
initiated as a scoping level trial using four primary leaching
factors, namely: leach temperature, slurry solids density,
hydrofluoric acid dosage and sulfuric acid dosage. DOE methods are
used to determine the effects of several factors at once and are
statistically analyzed to determine the effects of each factors,
i.e. acid dosage or temperature, also the interaction of two or
more factors on the system, i.e. temperature and slurry solids
density. Owing to the number of factors, a two-level factorial
design was used for the initial runs. Sixteen tests were run using
different combinations of Hi and Lo values for each of the factors.
All tests were run at atmospheric pressure with a leach time of
eight hours. Initial factor high and low levels were selected based
on similar unit operations currently used in the industry, i.e.
slurry solids density 20 to 50 percent, which is common in
flotation concentrate products and gold leach circuits,
respectively. Owing to the atmospheric leaching process, maximum
temperature considered was 100 degrees centigrade. Intermittent
samples were taken at two, four, and six hours and each solution
analyzed for pH, oxidation-reduction potential (ORP), and acid
concentration. For each test make-up, water and reagents were added
as required to maintain the DOE factor levels. At the termination
of the test, samples were filtered with dried solids and leach
solutions submitted for analyses. Statistical analysis of the
data was done using Stat-Ease's Design Expert and SAS' JMP
statistical analysis software.
Table 2: DOE
Parameter Matrix with Summary Agitation Leach Test Results, Iron
Point Master
Composite, for each of the 16 Tests
|
Test ID
|
Factor 1
Temp.,
⁰C
|
Factor 2
Density,
% solids
|
Factor 3
HF
g/L
|
Factor 4
H2SO4,
g/L
|
Leach
Time, hr
|
V
Recovery,
%
|
H2SO4
Consumption
kg/mt
|
|
DOE-1
|
Lo
|
Lo
|
Hi
|
Lo
|
8
|
47.3
|
115
|
DOE-2
|
Lo
|
Lo
|
Lo
|
Hi
|
8
|
48.9
|
189
|
DOE-3
|
Lo
|
Hi
|
Lo
|
Lo
|
8
|
21.3
|
103
|
DOE-4
|
Lo
|
Hi
|
Hi
|
Hi
|
8
|
53.5
|
170
|
DOE-5
|
Lo
|
Lo
|
Lo
|
Lo
|
8
|
33.7
|
122
|
DOE-6
|
Lo
|
Hi
|
Hi
|
Lo
|
8
|
33.0
|
99
|
DOE-7
|
Lo
|
Hi
|
Lo
|
Hi
|
8
|
44.0
|
102
|
DOE-8
|
Lo
|
Lo
|
Hi
|
Hi
|
8
|
65.7
|
N/A*
|
DOE-9
|
Hi
|
Hi
|
Hi
|
Hi
|
8
|
90.6
|
142
|
DOE-10
|
Hi
|
Lo
|
Lo
|
Hi
|
8
|
89.0
|
103
|
DOE-11
|
Hi
|
Hi
|
Lo
|
Lo
|
8
|
41.8
|
118
|
DOE-12
|
Hi
|
Lo
|
Hi
|
Lo
|
8
|
92.8
|
88
|
DOE-13
|
Hi
|
Hi
|
Hi
|
Lo
|
8
|
66.9
|
127
|
DOE-14
|
Hi
|
Lo
|
Lo
|
Lo
|
8
|
71.5
|
112
|
DOE-15
|
Hi
|
Hi
|
Lo
|
Hi
|
8
|
75.3
|
127
|
DOE-16
|
Hi
|
Lo
|
Hi
|
Hi
|
8
|
94.3
|
101
|
*Conditions for
DOE-8 are being re-run owing to anomalies with the acid balance
results.
|
Table 2 shows the high and low level for each of the tests, as
well as two of the primary responses, namely vanadium recovery
percentage and sulfuric acid consumption. Highlighted areas
correspond to the upper quartile of vanadium recovery, i.e. the top
four tests. The highest vanadium recoveries are associated with
some combination of higher sulfuric acid dosage and temperature.
The best four combinations average 91.7% vanadium recovery with the
highest recovery of 94.3% associated with a low percentage of solid
solution, and higher temperature and acid dosage. The upper
quartile vanadium tests show acid consumptions ranging between 88
kg/t and 142 kg/t with an average of 109 kg/t.
The high temperature runs consistently outperformed the low
temperature runs with respect to vanadium. Acid dosages have a
lower level of impact than temperature on recovery. High solids
density has a negative influence on the recovery, though not as
statistically significant as temperature or sulfuric acid
dosage.
Phase II Testing Underway
Further testing is underway that will better define operating
parameters required to develop an economic atmospheric leaching
process. It should be noted that the initial DOE runs are not
optimized. Supplemental testing is in progress to augment the
initial DOE with additional runs to optimize the leach parameters.
It is expected that improvements in recovery and acid consumption
are likely.
Testing of several samples spatially distributed throughout the
deposit and at different vanadium grades, will also be completed
("variability testing") to confirm metallurgical responses
throughout the deposit. Results of the variability testing will be
used to develop the geometallurgical model for the Iron Point
deposit and support the engineering and design process.
Additionally, bulk samples will be used to generate pregnant leach
solution for subsequent solvent extraction and vanadium
precipitation testing. Owing to the nature of the Victory leach
process, downstream processing of the vanadium rich solutions will
be via a commercially proven process to produce a high grade
V2O5 product.
Qualified Person
The scientific and technical information in this news release
has been reviewed and approved by Jeffrey L. Woods, B.Sc.,
SME-QP, MMSA-QP, who is a Qualified Person as defined by National
Instrument 43-101.
About Victory Metals
Victory owns a 100% interest in
the Iron Point Vanadium Project, located 22 miles east of
Winnemucca, Nevada. The project is
located within a few miles of Interstate 80, has high voltage
electric power lines running through the project area, and a
railroad line passing across the northern property boundary. The
Company is well financed to advance the project through resource
estimation and initial feasibility study work. Victory has a proven
capital markets and mining team led by Executive Chairman
Paul Matysek. Major shareholders
include Casino Gold (50%), and management, directors and founders
(25%). Approximately 51% of the Company's issued and outstanding
shares are subject to an escrow release over three
years.
Please see the Company's website at www.victorymetals.ca.
On Behalf of the Board of Directors of
VICTORY METALS INC.
Paul Matysek
Executive Chairman and Director
Neither the TSX Venture Exchange nor its Regulation Services
Provider (as that term is defined in the policies of the TSX
Venture Exchange) accepts responsibility for the adequacy or
accuracy of this release.
Forward-Looking Information
This news release contains certain forward-looking
information and forward-looking statements within the meaning of
applicable securities legislation (collectively "forward-looking
statements"). Certain information contained herein constitutes
"forward-looking information" under Canadian securities
legislation. Generally, forward-looking information can be
identified by the use of forward-looking terminology such as
"expects", "believes", "aims to", "plans to" or "intends to" or
variations of such words and phrases or statements that certain
actions, events or results "will" occur. Forward-looking statements
are based on the opinions and estimates of management as of the
date such statements are made and they are subject to known and
unknown risks, uncertainties and other factors that may cause the
actual results, level of activity, performance or achievements of
the Company to be materially different from those expressed by such
forward-looking statements or forward-looking information,
including the business of the Company, the speculative
nature of mineral exploration and development, fluctuating
commodity prices, competitive risks, and delay, inability to
complete a financing or failure to receive regulatory approvals.
Although management of the Company has attempted to identify
important factors that could cause actual results to differ
materially from those contained in forward-looking statements or
forward-looking information, there may be other factors that cause
results not to be as anticipated, estimated or intended. There can
be no assurance that such statements will prove to be accurate, as
actual results and future events could differ materially from those
anticipated in such statements. Accordingly, readers should not
place undue reliance on forward-looking statements and
forward-looking information. The Company does not undertake to
update any forward-looking statements or forward-looking
information that are incorporated by reference herein, except as
required by applicable securities laws.
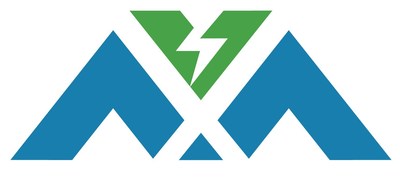
View original content to download
multimedia:http://www.prnewswire.com/news-releases/victory-metals-demonstrates-over-90-vanadium-recovery-using-a-hydrometallurgical-leach-process-at-the-iron-point-project-nevada-300833504.html
SOURCE Victory Metals Inc