The
information communicated within this announcement is deemed to
constitute inside information as stipulated under the Market Abuse
Regulations (EU) No. 596/2014 which is part of UK law by virtue of
the European Union (withdrawal) Act 2018. Upon the publication of
this announcement, this inside information is now considered to be
in the public domain.
12
November 2024
Neometals
Ltd
("Neometals" or "the
Company")
Positive Results from ELi™
Pilot Trial
Highlights:
· ELiTM has achieved the objectives of the pilot
stage of its electrolysis technology readiness;
· The
crystallisation trial produced high purity lithium hydroxide
monohydrate crystals and will produce further samples for market
evaluation;
· The
electrolysis trial data supports the expected power consumption and
membrane life assumptions, and hydrodynamic testing confirmed the
equipment can be applied to commercial-scale operation;
· The
final stages of the Pilot trial involved a 1,000-hour electrolysis
test of a lithium chloride solution (South American brine source),
purified with ELi™ technology and crystallisation of the lithium
hydroxide product;
· The
ELi™ Process potentially delivers users a step-change reduction in
operating costs to convert lithium chloride brines to lithium
hydroxide (or carbonate) with electrolysis, virtually eliminating
bulk reagents.
Sustainable process technology
developer, Neometals Ltd (ASX: NMT & AIM: NMT) ("Neometals" or "the Company"), is pleased to announce the
results of the final electrolysis and crystallisation stages of the
ELi™ Process ("ELi™") Pilot trial ("Trial"). ELi™ is owned by Reed Advanced Materials
Pty Ltd ("RAM"), a 70:30
incorporated joint venture between Neometals Ltd and Mineral
Resources Ltd.
The technology uses electricity to
convert lithium chloride solutions into lithium hydroxide in a
conventional chlor-alkali cell, replacing the need for large
volumes of bulk chemical reagents required in the
industry-standard, chemical precipitation process. ELi™ has the potential to deliver users a
step-change in operating costs[1] versus industry standard chemical
precipitation.
RAM completed a long-duration
1,000-hour electrolysis membrane durability test utilising a
lithium chloride solution produced in the successful 2023
'purification' trial on brine sourced from South
America[2]. The Trial
tested the performance of the electrolysis cell membrane over a
duration five times longer than historic tests and the results
support current estimates of two major variable operating costs
(power consumption and membrane life) and successfully produced
lithium hydroxide monohydrate ("LHM") of very high purity.
Table 1 - LHM Sample
Analysis
Element[3]
|
LiOH %
|
CO32-%
|
Na
ppm
|
Ca
ppm
|
K
ppm
|
Fe
ppm
|
SO4 ppm
|
Target Spec
|
>56.5
|
<0.4
|
20
|
10
|
10
|
10
|
100
|
Sample 1
|
56.6
|
ND
|
1.8
|
6.0
|
5.6
|
8.2
|
2.4
|
Sample 2
|
56.9
|
ND
|
3.6
|
9.7
|
5.1
|
8.6
|
1.5
|
Additionally, further samples are
being produced for qualitative evaluation.
These results are significant as
they confirm or exceed historic results achieved from processing
synthetic brine solutions (from commercial lithium chloride
crystals) at continuous laboratory scale on less-pure eluate from
natural brine, at a pilot scale and over a longer duration. The
increased confidence in major operating cost inputs supports the
potential operating cost advantage of the ELi™ process in the
conversion of lithium chloride brines and is a major milestone in
the commercialisation of the technology under a low-capex, low-risk
technology licensing business model to generate future royalty
income. RAM holds 19 granted patents in the principal lithium
producing jurisdictions and has a further 14 pending national phase
patents at various stages of prosecution globally.
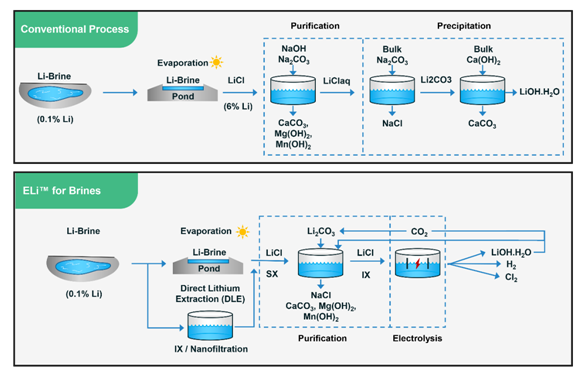
Figure 1 - Schematic comparison flowsheet of the
conventional lithium hydroxide from brines vs the patented ELi™
process.
ELi™ Electrolysis Pilot Trial Results
The current efficiency for the Trial
averaged approximately 74% and trended upwards during the course of
testing, consistent with historical electrolysis results on
synthetic brine solutions. The current efficiency measures the
actual catholyte produced as a percentage of the maximum possible
production and, pleasingly, the results support the electricity
consumption assumption in the 2023 Engineering Cost
Study[4].
The Trial membrane was physically
inspected and chemically analysed following completion of testing,
to determine the extent of any deterioration which may have arisen
during the tests. The membrane was observed to be in excellent
condition and no significant build-up of elements was identified in
the membrane destructive digestion test. A shorter 40-hour duration
test examined the hydrodynamic performance and polarisation
characteristics of a full-height commercial electrolysis cell. This
test successfully confirmed the flowsheet can be applied to
commercial-scale electrolysis cells. This outcome gives confidence
this is an effective means of producing a suitable solution for
production of battery grade lithium hydroxide monohydrate
("LHM").
The lithium hydroxide catholyte from
electrolysis was processed in the crystallisation trial to produce
LHM final product. Sample splits of the product were sent for
analysis in separate laboratories, in South Africa and Australia.
The Australian analytical laboratory is considered to have greater
reliability in determinations of very low concentration impurities
(in low ppm and in ppb-level concentration of impurity elements),
so the Australian laboratory results for impurities are reported.
Some carbonation of the sample sent to the Australian laboratory
was observed in the analysis, but this has been traced to the
sample not having been packed in an inert atmosphere and aging in
transit to Australia. Lithium hydroxide readily carbonates by
absorbing the carbon dioxide in air but contact with air does not
change the content of other impurities. The sample sent to the
South African laboratory was not exposed to ambient carbon dioxide
and analysis did not detect any carbonation in the sample. The
South African laboratory lithium hydroxide and carbonate results
are considered reliable and are reported.
The combined analysis results meet
the target specifications listed in Table 1. Sample product is
being produced for further evaluation by both RAM and the owner of
the South American brine source.
Forward Plan
ELiTM has satisfied the
objectives of the pilot stage of its electrolysis technology
readiness. RAM has prepared an information memorandum and data room
to commence a formal industrial partner selection process, with the
aim of advancing the technology through industrial validation, in
demonstration plant trials.
RAM continues to evaluate
third-party brine samples and to advance discussions with
chlor-alkali plant manufacturers in relation to preferred vendor
relationships.
Authorised on behalf of Neometals by
Christopher Reed, Managing Director.
- ENDS
-
For more information, please
contact:
Neometals Ltd
|
|
Chris Reed, Managing Director &
Chief Executive Officer
|
+61 8 9322 1182
|
Chris Kelsall, CFO & Company
Secretary
|
+61 8 9322 1182
|
Cavendish Capital Markets Ltd - NOMAD &
Broker
|
|
Neil McDonald
|
+44 (0)131 220 9771
|
Peter Lynch
|
+44 (0)131 220 9772
|
Adam Rae
|
+44 (0)131 220 9778
|
|
|
About Neometals
Neometals facilitates sustainable
critical material supply chains and reduces the environmental
burden of traditional mining in the global transition to a circular
economy.
The Company is commercialising a
portfolio of sustainable processing solutions that recycle and
recover critical materials from high-value waste
streams.
· Neometals' core focus is its patented, Lithium-ion Battery ("LiB")
Recycling technology (50% NMT), being commercialised
in a 50:50 incorporated JV (Primobius GmbH) with 150-year-old
German plant builder, SMS group GmbH. Primobius is supplying
Mercedes-Benz a 2,500tpa recycling plant and operates its own LiB
Disposal Service in Germany. Primobius' first 21,000tpa commercial
plant will be offered to Stelco under an existing technology
licence for North America.
Neometals is developing two advanced
battery materials technologies for commercialisation under
low-risk, low-capex technology licensing business
models:
· Lithium Chemicals (70%
NMT) - Patented ELi™ electrolysis
process, co-owned 30% by Mineral Resources Ltd, to produce battery
quality lithium hydroxide from brine and/or hard-rock feedstocks at
lowest quartile operating costs. Successfully completed pilot scale
test work and planning further development with industrialisation
partners under a technology licensing business model;
and
· Vanadium
Recovery (100%
NMT) - Patent pending
hydrometallurgical process to produce high-purity vanadium
pentoxide from steelmaking by-product ("Slag") at lowest-quartile
operating cost and carbon footprint. Planning to exploit under a
technology licensing business model. Project financing process for
first commercial plant in progress.
For further information, visit: www.neometals.com.au.